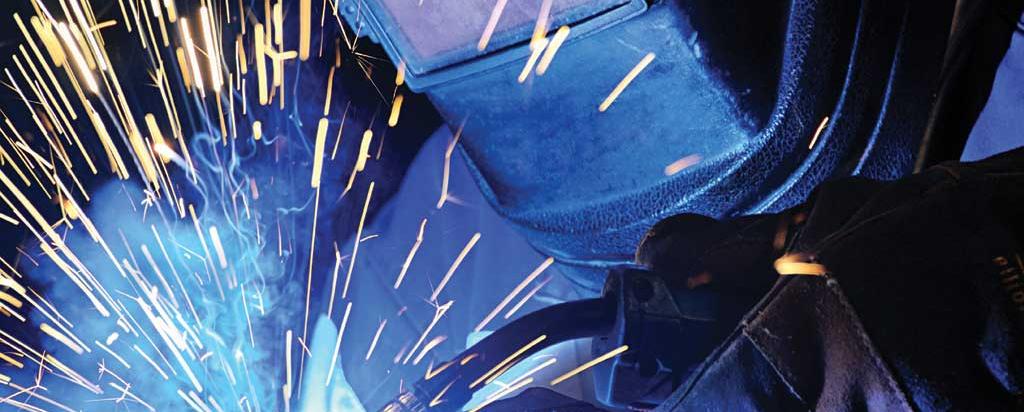
Applications - Kowari
The residual stress diffractometer can be used to reveal residual stresses: in thermo-mechanically processed metals (e.g. products of rolling process):
Thermo-mechanically processed metals (e.g. products of rolling process) |
|
Different welded components, including dissimilar metal welding, joined using different methods |
|
Bulk components produced by different material deposition techniques |
|
Bulk multi-phase and composite materials |
|
Thick (1-10mm) and thin (200-1000 μm) coatings (metal, ceramic, composite) such as thermal barrier, wear resistant and corrosion resistant made by different technique |
|
Components treated with different surface treatment techniques |
|
Geological material |
|
The following material science physical phenomena can be studied in the residual stress experiment:
- Stress corrosion cracking due to extreme environments :
- Heat and pressure/stress (pressure pipes of power generators) - Corrosive environment and stress (pipelines, steel reinforcement in concrete) - Fatigue, crack growth and development in materials undergoing external loading or contact stress in structural components or load-bearing parts.
- Shape-memory alloys - these materials can return to their original shape after bending or deformation (e.g. vascular stents) and are used in medical and aerospace applications.
- In-situ plastic deformation experiment can reveal information on details of deformation mechanism of material (activation of slip systems, dynamic recrystallization, etc.). Frequently, this experiment is done using elevated temperatures and different rates of deformation.
- Creep, in spite of necessary time commitments, also can be studied, especially high temperature creep at constant load.
- Texture formation can be routinely studied using our Eulerian cradle
Recent results
Highlights