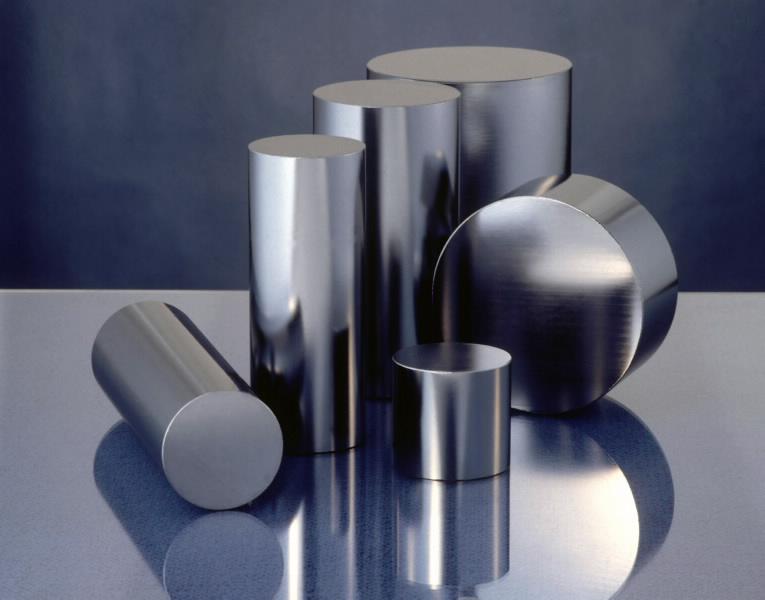
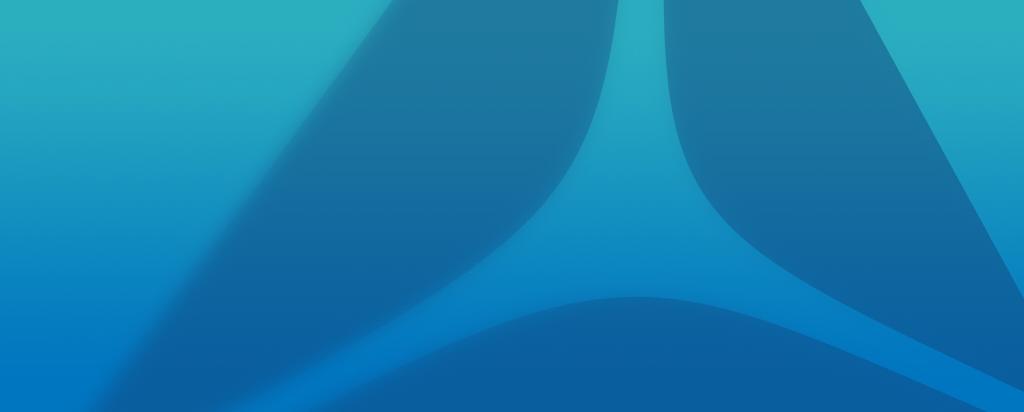
Published on the 1st June 2015 by ANSTO Staff
ANSTO’s business operations are a thriving component of an organisation on the brink of expansion to meet global demand for nuclear products. The evolution of ANSTO Silicon into a competitive, profitable and reliable provider of Silicon Neutron Transmutation Doping (NTD) services to international markets is an example of a clear strategy which has been implemented well through planning and control.
![]() The combined operational excellence program of the Nuclear Business Division, which includes ANSTO Silicon, has delivered export growth and improvements across the whole supply chain. Business improvements resulted in a Class A accreditation for Planning and Control from the international planning consultants group, Oliver Wight. Today ANSTO Silicon is one the world’s main suppliers of irradiated silicon which is used in the high end electronics market. There has been a significant increase in market share since 2007. In 2014 ANSTO Silicon delivered 49.9 tonnes to the market. Approximately ninety-five per cent of the product was delivered in full on time. “ANSTO is a reliable supplier of high quality products and services to our customers,” said Shaun Jenkinson, Group Executive for Nuclear Business. Irradiated silicon is primarily used in advanced, high and very high power devices, such as high power semi-conductors, diodes and several other classes of transistors for the transportation, energy infrastructure and industrial sectors. The Utilisation Section at ANSTO is responsible for effectively optimising the facilities in the Open Pool Australian Light water (OPAL) reactor to produce irradiated silicon, Molybdenum-99 and other isotopes. The team works closely with the Operations Section, which manages all aspects of running the nuclear reactor, including ensuring the flow of neutrons to research instruments. Because there is considerable activity at the reactor, getting the timing of utilisation activities is crucial. Silicon ingots have to be lowered into six specialised facilities in the reactor pool by an operator who is positioned on a mobile bridge above the pool. Irradiation times for the silicon ingots can vary from one hour to five days, depending on the level of resistivity required by the silicon manufacturer. When the required parameters specified by the customer are achieved, the silicon can with irradiated silicon inside is removed from the facility by highly skilled utilisation operators, who transfer it to the adjacent service pool using a hoist attached to Operations Bridge. The irradiated silicon “cools” by radiation decay and stops emitting radiation approximately 48 hours after irradiation. Then it is removed from the service pool using a dedicated unloading station. The final step is to ensure that the silicon ingots are clean and ready for final inspection before shipping to the manufacturer. Stringent scheduling to meet the customer’s needs was essential in improving efficiencies in the silicon production process. Scheduling silicon irradiation is complicated by the need to integrate with the reactor operations schedule, and the production of Molybdenum-99 and other isotopes. Production Manager, OPAL Utilisation, Rasmi Fraihat points out that identifying and controlling the process variables, integrating all customer demands in one schedule and mapping all the tasks in a graphical representation, has helped greatly in improving overall efficiency. “Getting the production schedule right has been crucial in improving utilisation,” explained Rasmi Fraihat. “But it was the commitment of everyone in the team that made it all work.” A utilisation team of 15 works in shifts (3 workers per shift) over 24 hours 7 days a week - supported by a day team. On average, the silicon production is scheduled one week ahead. There is continuous liaison with the ANSTO Silicon business team about the progress of silicon production to ensure client needs are met. ANSTO began irradiating silicon in the late 1980s using the HIFAR reactor, which is no longer operational.
|