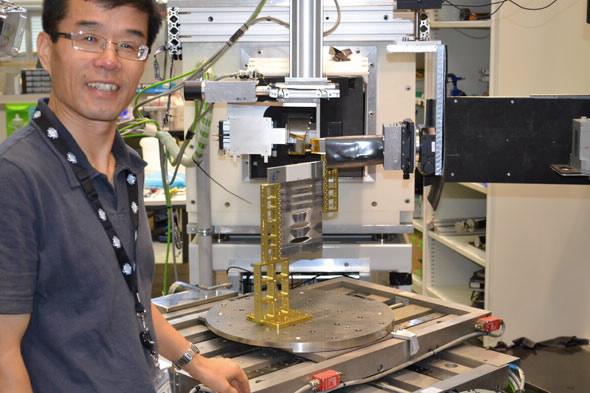
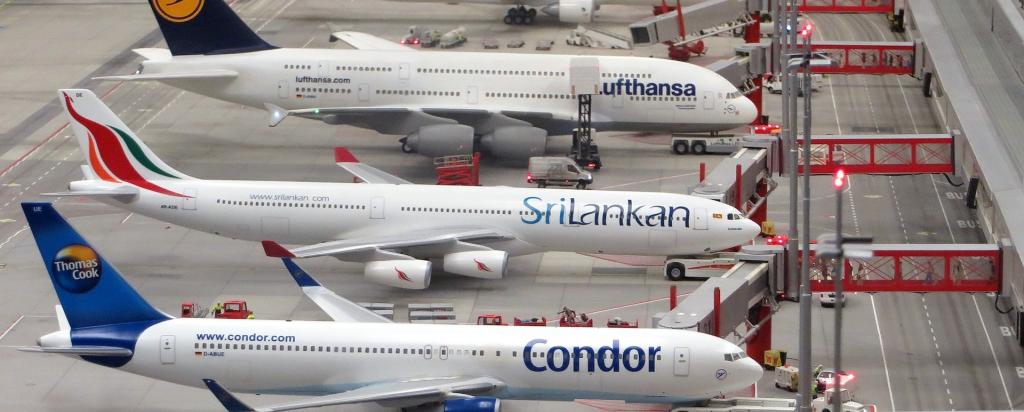
Published on the 13th August 2015 by ANSTO Staff
Fatigue and corrosion damage to structural components can be a major threat to the safety and airworthiness of civil and military aircraft, particularly those pushed past their initial design fatigue life.
ANSTO researchers have used nuclear techniques to evaluate a technology to repair corrosion and fatigue damage on the structural components of aircraft in collaboration with research scientists and engineers from Aerospace Division of Defence Science and Technology Group (DST Group).
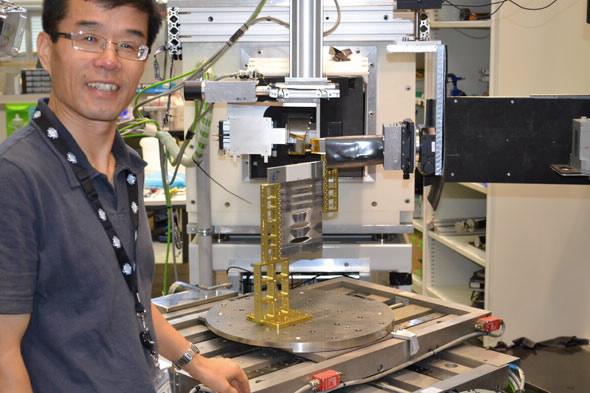
Bragg Institute Senior Research Scientist and Industrial Liaison Manager Anna Paradowska was part of a research team led by DST Group’s Dr Wyman Zhuang (pictured above) that evaluated structural repair technologies including supersonic particle deposition and laser cladding with post repair surface enhancement technology to extend the fatigue life of the aircraft. Paradowska used neutron diffraction on the Kowari strain scanner for residual stress analysis. The DST Group team tested fatigue performance of the specimens made of aircraft structural materials with various repair and post-repair enhancement conditions, and examined the fatigue cracking in the specimens after the fatigue testing using scanning electron microscopy.
The research, which was published in Applied Surface Science in September 2014, confirmed deep surface rolling improved fatigue performance.Residual stresses are internal stresses remaining within an object when there are no external forces acting upon it. “Residual stresses that are found in materials and components are one of the most important factors impacting the fatigue performance of aircraft structural repairs,” said Zhuang. The deep surface rolling can introduce beneficial compressive residual stresses in the repair area that enhance the fatigue performance of repaired components.
Aircraft structural repair:
The maintenance of ageing aircraft includes the repair of corrosion and wear, and the restoration of geometry and strength. DST Group research demonstrated the potential of advanced repair technologies for ensuring continued airworthiness and improving aircraft availability—including the surface enhancement known as deep surface rolling (DSR).
Zhuang’s team at Aerospace Division in DST Group developed and applied deep surface rolling, laser cladding, and post heat treatment on samples of aluminium alloy 7075-T651 plates. Aluminium 7000 series alloys are used extensively in the aerospace industry because of their high strength to density ratio and corrosion resistance. The material has been the standard workhorse within the aerospace industry since its introduction in 1943. The 7000 series of alloys are comprised mainly of aluminium, zinc, magnesium and copper with small quantities of other elements.
Laser cladding was used to deposit aluminium-silicon powders onto the damaged surface of the sample component. A relatively narrow Heat-Affected Zone develops in aluminium alloys that are repaired with this method.
Post-heat treatment following laser cladding was used to reduce detrimental tensile residual stresses and regenerate precipitation hardening.
In deep surface rolling a high pressure fluid floats a rolling ball in a socket as it presses and rolls freely along the surface of a component with sufficient force and repetitive deformation to deliberately create both a cold worked surface as well as a beneficial compressive layer of residual stress.
Neutron diffraction residual stress analysis:
Following treatment, Paradowska and the DST Group team used neutron diffraction on the Kowari strain scanner to measure the 3-dimensional residual stresses on the several samples with various process parameters.
“We used this instrument because it can provide sub-surface information of residual stresses without the destruction of the specimens but with high resolution measurements. Often this information cannot be obtained by other techniques. Neutrons are capable of penetrating deep into materials to acquire data about localised stresses in the deformed material. This powerful tool gives researchers a unique capability to study the same specimens going through various stages of manufacturing process” explained Paradowska.
Residual stress can be measured by neutron diffraction using the distance between the atoms in crystalline materials.
In this research the neutron diffraction measurements captured the hydrostatic stresses and indicated that deep surface rolling caused deeper and higher magnitude compressive residual stresses at the surface and beyond it into the substrate. These stresses increase both the yield and ultimate strength of the material which improve fatigue strength.
Fatigue tests confirmed that deep surface rolling increased the average fatigue life more than five times compared with just laser clad specimens, while post heat treatment only increased fatigue life by 40 per cent.
“Structural integrity requirements for aircraft parts are of the highest level. The repaired components need to demonstrated that the restored component shall have a structural strength condition, equivalent or better than its original configuration, “said Zhuang.
DST Group researchers used scanning electron microscopy for fractographic analysis. The examination confirmed that deep surface rolling improved the microstructure of the specimens.
In this regard, a strict certification road path, including repair analysis to achieve a technology readiness level has been developed by DST Group team. Any new repair process has undergo an extensive repair analysis in order to ensure there is compliance with existing certification for the aircraft. The new repair process must also be verified by analysis, inspections and or/tests that determine the readiness level of the technology. The test program includes metallurgical analysis, static and fatigue testing, and evaluating the durability of coatings. The goal is to restore any damaged structure to a standard that recovers its design capability over its remaining full service life.
ANSTO has a research agreement with the DST Group to collaborate on a number of projects, including a government radiological and nuclear spectrum database to help counter threats to Australia’s national security.
References included in original paper: doi:10.1016/j.apsusc.2014.09.139