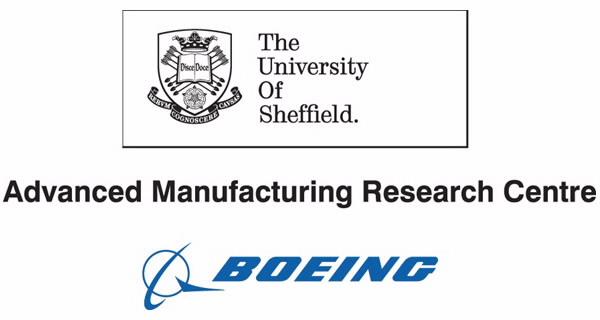
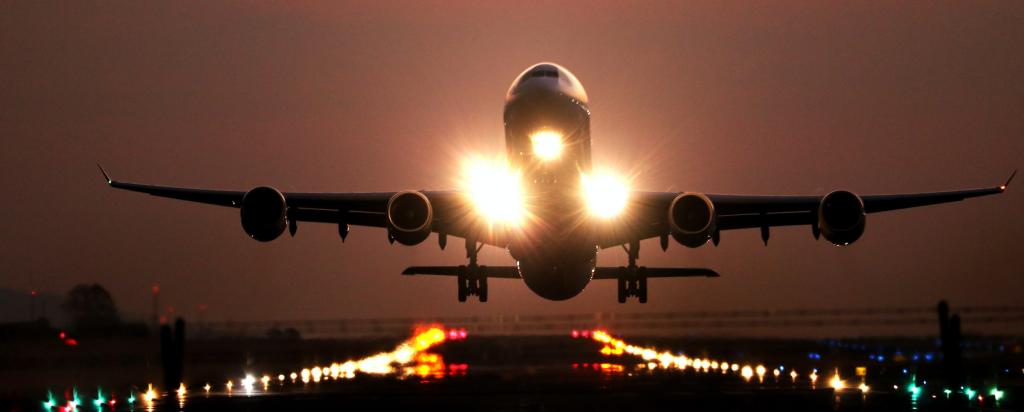
Published on the 5th October 2016 by ANSTO Staff
ANSTO and the University of Sheffield Advanced Manufacturing Research Centre (AMRC) with Boeing have recently used the KOWARI strain scanner to understand the residual stress distribution in large scale Aluminium billets used to manufacture modern aerospace components.
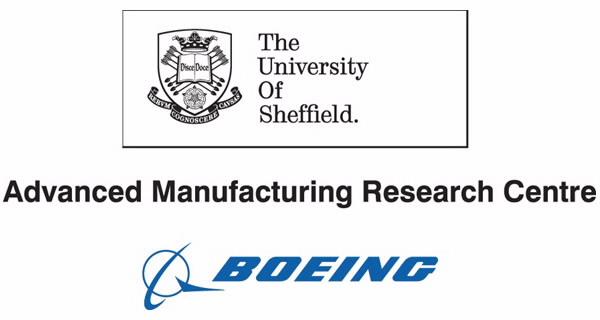
The AMRC with Boeing is a world-class centre undertaking research into advanced manufacturing technologies used in the aerospace, automotive, medical and other high-value manufacturing sectors. The AMRC has a global reputation for helping companies overcome manufacturing problems and is a model for collaborative research involving universities, academics and industry worldwide. Combining state of the art technologies with the AMRC’s expertise in design and prototyping, machining, casting, welding, additive manufacturing, composites and structural testing, has created a manufacturing resource far beyond anything previously available in the UK. The AMRC is a member of the High Value Manufacturing Catapult, a consortium of leading manufacturing and process research centres, backed by the UK’s innovation agency, Innovate UK.
These measurements are a part of large-scale investigations carried out by the AMRC and partners to develop cost-effective manufacturing procedures for safe and reliable aerospace components. Understanding the development and distribution of residuals stresses during manufacturing is a key factor in the development of methods to minimise distortions in components during machining. The experiment is a result of ongoing project collaboration of the KOWARI team with Dr Ravi Bilkhu from the Process Modelling and Residual Stress Measurement Groups at AMRC with Boeing.