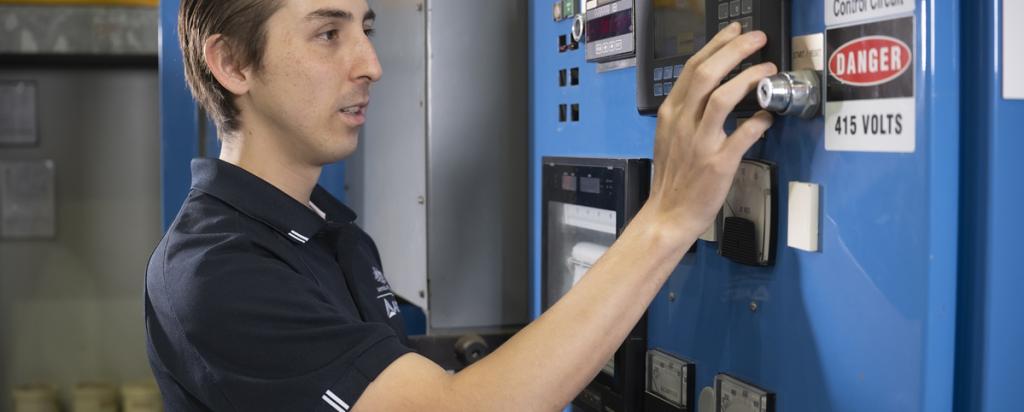
Hot Isostatic Pressing - case study
The challenge
Titanium (Ti) is one of the most important materials for demanding engineering applications and is used extensively in aerospace, automotive, petrochemical and biomedical industries. Its high strength-to-weight ratio, good mechanical properties, excellent corrosion resistance and biocompatibility make it highly desirable.
Despite having robust characteristics and promising applications, titanium is naturally difficult to process into engineered materials with complex designs, given its high chemical reactivity and high sensitivity to oxygen, which can lead to difficulties in processing, fabrication, and metallurgical bonding.
Additive Manufacturing (AM), particularly cold spraying, provides significant advantages over traditional subtractive methods, including shorter lead times, improved mechanical performance, and reduced manufacturing costs. However, in the aerospace industry, it is imperative to address the challenge of controlling porosity in AM-fabricated titanium components. Maintaining a low porosity level is essential to ensure structural integrity and meet the stringent requirements of aerospace applications.
The solution
Hot Isostatic Pressing (HIPing) is often specified as the recommended thermal processing step to meet quality and performance benchmarks for aerospace applications. This process is not only useful to reduce porosity, but also can modify microstructures to enhance mechanical properties.
ANSTO has two HIPs available for advancing materials and process development, a small-scale system for feasibility assessment and a larger scale HIP for industrially relevant scale parts. Both operate to a maximum pressure of 200 MPa in an argon atmosphere. HIPing with appropriately chosen parameters, temperature, pressure, and isothermal hold time, can help to reduce internal stress, reduce porosity and refine the microstructure. The HIPing facility at ANSTO also operates laboratories and provides other technical support to qualify and characterise the performance of materials before and after the thermal treatment process.
The impact
Titomic, a global technology integration company, engaged ANSTO to use HIP on titanium samples manufactured by cold spray additive manufacturing to improve the materials performance of titanium components. Their aim is to create sovereign capability for the additive manufacture of titanium parts utilising cost-effective irregular morphology powder titanium (HDH) for Australian organisation such as the space industry & defence and international industries such as aviation.
A parametric study, using a suite of HIP heat treatment cycles were evaluated against performance criteria set by Titomic. The results showed that HIPing temperature plays a critical role in refining properties as it affects grain morphology, as well as the size and shape of porosity — which all impact the performance of the material. HIPing decreased the amount of porosity within the samples regardless of the sample size and geometry and substantially increased ductility due to changes to the grain size.
This case study underlines the crucial role of optimising cold spray process parameters in conjunction with post heat treatment, specifically through Hot Isostatic Pressing. By carefully tailoring the cold spray process variables and subsequently subjecting the components to an optimised HIP cycle, this comprehensive study demonstrated significant improvements to the performance of cold-sprayed pure titanium materials.
The tailored combination of process parameters and HIP post heat treatment led to a substantial reduction in the amount of porosity and a notable increase in ductility, effectively aligning the properties of the cold-sprayed components with those of the titanium alloy commonly used in aerospace applications. The outcome of this case study has ultimately enabled the realisation of high-performance and reliable components for critical aerospace needs.
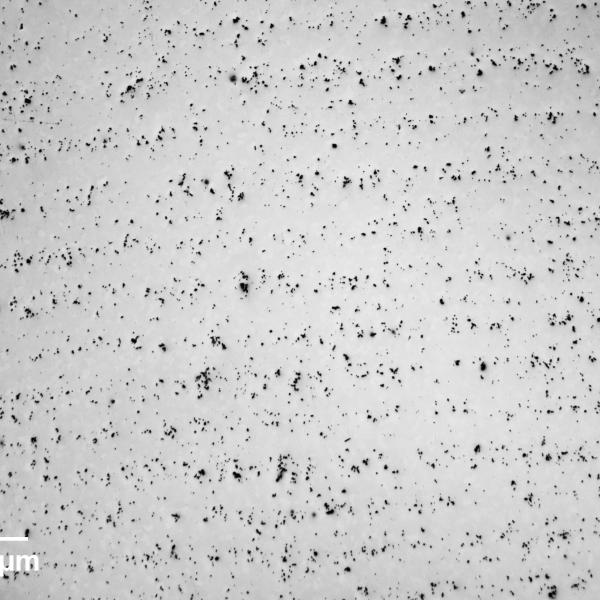
Figure 1. Cold Sprayed titanium sample before HIPing
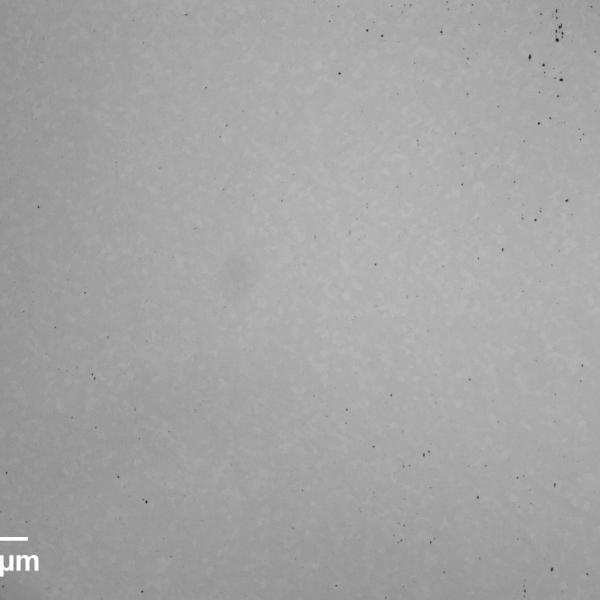
Figure 2. Cold Sprayed titanium sample with reduced porosity