
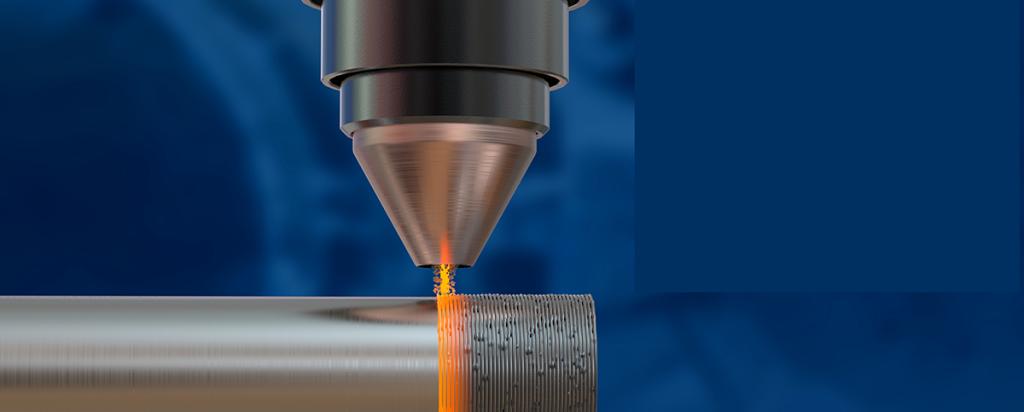
Published on the 8th March 2023 by ANSTO Staff
ANSTO is part of a team that received a High Commendation at the AVALON 2023 National Innovation Award for a collaborative project demonstrating sovereign industrial capability gains and delivering sustainment cost reductions for Defence.
DMTC Limited and its industry and research partners are pairing advances in the use of existing additive manufacturing technologies, such as laser additive deposition, with novel technology developments to successfully repair worn or degraded airframe components.
The team comprises Melbourne-based Rosebank Engineering, research expertise from Swinburne University of Technology and RMIT and scientists from Defence (DSTG) and ANSTO.
A/Prof Ondrej Muransky said that ANSTO was honoured to be part of the recognised team.
Our contribution focuses on developing multi-scale physics-based numerical models of additive manufacturing processes.
When it comes to the manufacturing and repairing of engineering components, broader adoption of additive manufacturing processes is hindered by an insufficient understanding of the relationship between process, microstructure and properties, which governs an in-service performance.
Understanding the ongoing thermo-physical, thermo-metallurgical, and thermo-mechanical processes taking place during additive manufacturing can address some of the long-standing challenges. This insight can reduce a component’s failure due to residual stresses, extensive distortion and/or microstructural defects.
An example of SYSWELD predictions of the final phase, hardness, and stress distributions on plane B for the LMD-3 deposition strategy
Laser metal deposition allows for a high deposition rate that enhances building and repairing larger engineering structures. The advantages make the laser metal deposition process an attractive manufacturing/repair process for many energy, aerospace and defence applications.
“Despite the major advantages of laser-based additive manufacturing processes, there is, however, a continuous need to develop a full understanding of the process-structure-property relationships,” explained A/Prof Muransky.
A multi-scale physics-based modelling framework is needed to elucidate the complex interdependencies between additive manufacturing process parameters and resulting residual stresses, distortion, and microstructure. This framework governs an in-service performance of additively-manufactured or additively-repaired engineering components.
The main emphasis is on developing an in-depth understanding of the effects of a large number of process variables of the ongoing metallurgical processes, residual stresses, and distortion, which result in mechanical and crack growth characteristics.
Capabilities that support the work include high-performance computing clusters, material testing, and material characterisation using microscopy, neutron scattering, and synchrotron techniques.
The numerical modelling team includes A/Prof Ondrej Muransky and Ms Wendy Ji.
ANSTO jointly works on the development of these advanced multi-scale physics-based models for the laser-based additive manufacturing process for energy, aerospace, and defence applications with Swinburne University of Technology, the Royal Melbourne Institute of Technology, Rosebank Engineering, and Defence Science and Technology Group under the auspices of the Defence Materials Technology Centre.
The developed numerical modelling framework will help in understanding of the process–microstructure–property relationship and advance the rapid optimisation of the additive manufacturing process for industrial applications.
The long view goal of the project is to develop validated numerical multi-scale physics-based models which can assist a large range of industries wishing to utilise additive manufacturing for manufacturing and repairs of engineering components.
Although Australian research priorities are currently under review, advanced manufacturing has been an Australian research priority since 2015.