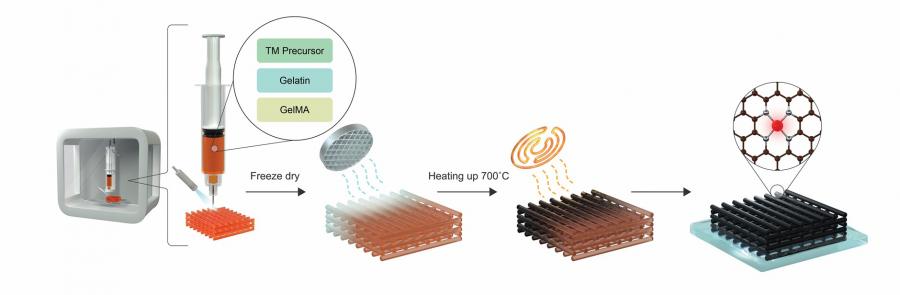
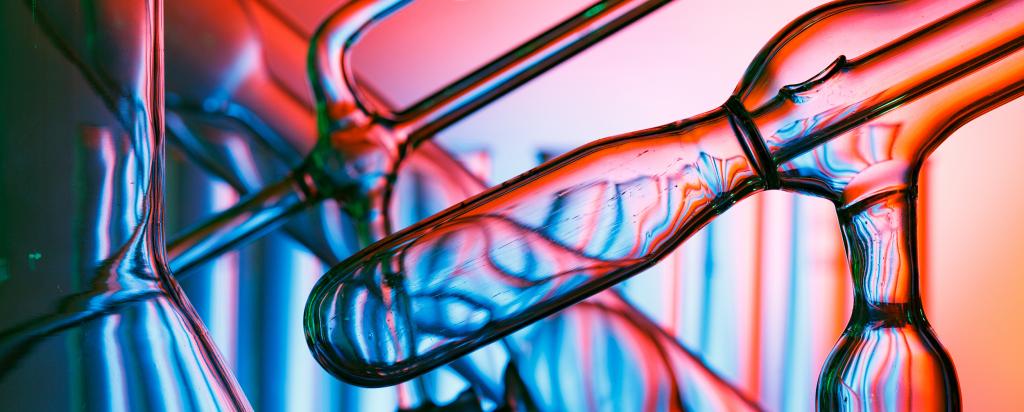
Published on the 1st January 2023 by ANSTO Staff
Key Points
-
A research team led by the University of Adelaide has developed a straightforward and cost-effective synthesising approach to produce single atom catalysts (SACs) using a 3D printing technique
-
SACs have broad industrial chemical and energy applications
-
Synchrotron technique confirmed the 3D printing technique had produced a material consisting of isolated single atom sites
A large international collaboration led by Prof Shizhang Qiao, an Australian Laureate Fellow at the University of Adelaide has developed a straightforward and cost-effective synthesising approach to produce single atom catalysts (SACs) using a 3D printing technique—potentially paving the way for large scale commercial production with broad industrial applications.
The research has been published in Nature Synthesis.
The team mailed in samples to the Australian Synchrotron during COVID lockdown for materials characterisation using the X-ray absorption spectroscopy (XAS) beamline.
A catalyst is a substance that designed to drive a specific chemical reaction to convert chemicals to other, less harmful, valuable industrial products. The efficiency at which a given catalyst aids the reaction is often found to be determined by its surface area.
For example, a bulk metallic cobalt foil may aid in chemical reductions, but the same number of cobalt atoms in the form of nanoparticles would be significantly more efficient given the greater surface area available for the reaction to take place.
Taken to its extreme, single atom catalysts (SACs) refer to individual metal atoms, not bonding to metal, but often dispersed uniformly on a fixed substrate (such as carbon), offering the highest possible value of atom economy.
The ideal atom economy, known as 100% atom economy, for a chemical reaction is a process in which all reactant atoms are found in the desired product.
The isolated metal atoms have unique and novel physical and chemical properties, driving efficient and tailored catalytic reactions with extremely high catalytic activity.
However, current production methods of wet-chemical processes, mechano-chemical abrasion, thermal shockwave, and laser irradiation are considered complex, costly and impractical for mass production.
“We have developed a synthesis approach that allows the use of 3D printing to fabricate single-atom catalysts. Our method has the potential to be more cost-effective and simpler than current approaches,” explained by Prof Qiao.
3D printing allows the customisation of geometric designs from millimetres to metres, which is important for industrial applications.
The combination of 3D printing and single-atom catalysts provides a promising but simplified way to manufacture SACs at different scales.
“This novel combination has the potential to advance Australia’s status as a global leader in tackling the effects of climate change and help us take the lead in new techniques to make chemicals that benefit society,” said Prof Qiao.
Senior scientist Dr Bernt Johannessen, also a co-author on the paper and long-time collaborator, carried out measurements on the XAS beamline for the research team across multiple beamtime allocations (and multiple COVID lockdowns).
“Pleasingly, we were able to confirm that the 3D printing technique had produced a material consisting of isolated single atom sites as opposed to nanoparticles or clusters of atoms. The instrument allows us to differentiate between cobalt bonding to light elements, like carbon, or cobalt bonding to other cobalt to form nanoparticles,” confirmed by Dr Johannessen.
“The larger clusters you have, the less effective they will be as single atom catalysts, so the confirmation of isolated nature of single-atom sites is crucial to the project conclusions and potential industrial applications.
“The XAS Beamline at ANSTO has been integral to a number of high-profile studies in this field over the past several years now, and we are looking forward to seeing how our user community continues to grow over the years ahead.”
Other participating organisations included the University of Otago, and the Chinese Academy of Sciences.