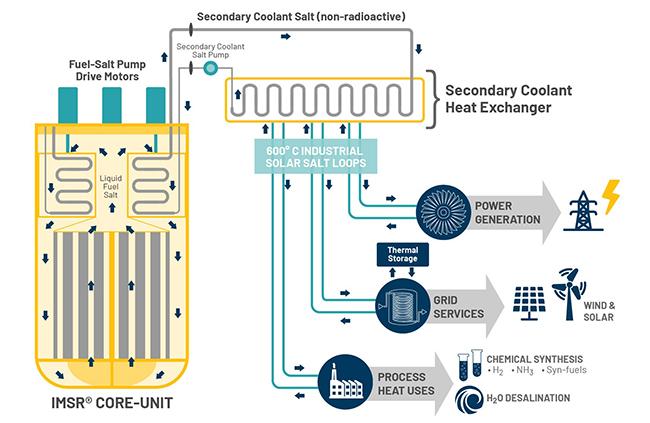
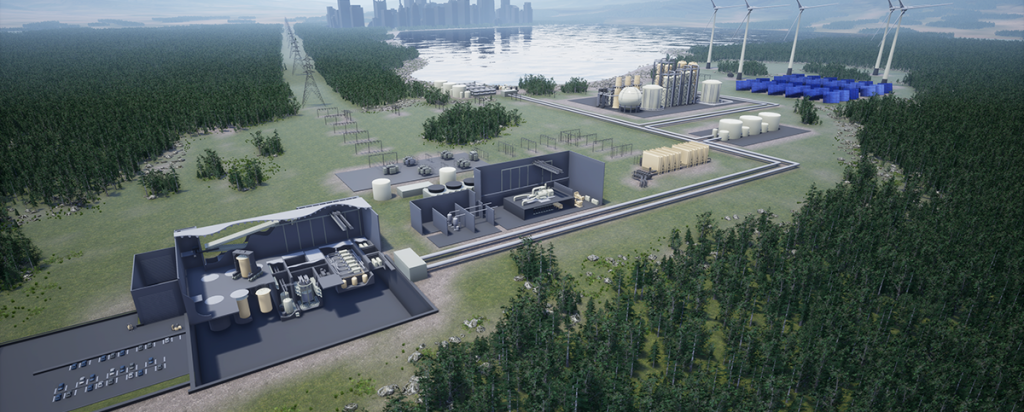
The evolution of molten salt reactors
Although there are many new designs for molten salt reactors today, the history of the development of molten salt-based reactor systems dates back to the 1950s.
The nuclear industry was the first to recognise the potential of molten-salt-based energy-generation systems in the 1950s during the U.S. Aircraft Nuclear Propulsion Program.
This program, which was later abandoned, led to the Molten Salt Reactor Experiment at Oak Ridge National Laboratory, which demonstrated the viability of energy-generating using molten salt reactor (MSR) technology.
Advantages of new molten salt-based reactor systems
The main advantages of MSRs stem from the thermo-physical properties of molten salts: high boiling point, low viscosity, low vapour pressure, high thermal conductivity, and high volumetric heat capacity.
The high boiling point and low vapour pressure are of interest because of the operational safety of a molten-salt-based system at atmospheric pressure, and favourable heat transfer characteristics that enable efficient and economic energy transfer and storage.
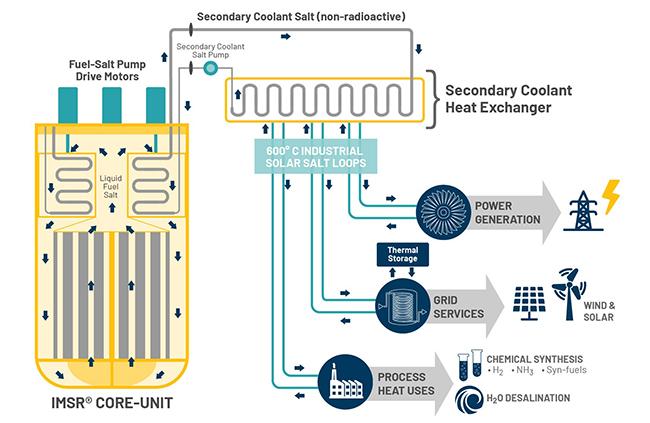
The ISMRR molten salt reactor system under development
These systems are inherently safe because any breach of the reactor containment vessel leads to the solidification of the salt, which would prevent an uncontrolled release of radioactive material.
MSRs offer unmatched design flexibility, as they can vary in size and power output, utilise a variety of fuels including plutonium-239, uranium-235, and uranium-233 bred from thorium, and they operate with both thermal and fast neutron spectrums.
While thermal MSRs maximise the utilisation of fuel, fast MSRs minimise nuclear waste–bringing significant advantages for proliferation-resistance and waste minimisation.
And, owing to their inherent load-following capabilities, the proposed MSR systems provide unmatched operational flexibility given they can operate in remote areas as well as in existing complex electricity networks.
MSRs can complement the intermittency of renewable energy generation, in turn, promoting a low-emissions hybrid renewable-nuclear energy network.
Today MSRs hold the promise of being one of the most efficient energy-generation systems, even when compared to the current Light Water Reactor (LWR) systems, which are part of Generation III+ reactors.
This is demonstrated by the Energy Return on Investment (EROI) coefficient, which is simply a ratio of the energy output (Eout) and energy input (Ein).

At the level of Government, the current research and development of MSR systems is overseen by the Generation IV International Forum (GIF). Australia joined this international effort in 2017 by signing the GIF Framework Agreement. ANSTO is the implementing agency for Australia.
Government agencies were joined by a number of start-up companies, including Terra Power, Terrestrial Energy and Moltex, among others. Some of these companies pursue the development and near-future deployment of commercially-available MSR systems independently.
With a rapidly evolving space industry, there is a renewed interest in MSR systems for nuclear electric propulsion, as well as extra-terrestrial surface power.
The nuclear industry and other relevant government organisations are pursuing molten-salt-based energy-generation systems focused predominantly on electricity and industrial heat production and, potentially, propulsion.
The renewable energy-generation industry has built on a decades-long effort by developing molten-salt-based Thermal Energy Storage systems to combat the intermittency of renewable energy generation.
Challenges today
The widespread deployment of molten-salt-based energy-generation and energy-storage systems has been hindered predominantly by the development and standardisation of suitable structural materials.
These materials are required to withstand a combination of challenging environmental conditions, including highly corrosive molten salts, high operating temperatures, and damage from high energy particles created by the ongoing fission process.
In addition, a number of challenges exist with respect to the supply chain, remote operation, tritium production, and the complex chemical processes required for fission product separation.
These challenges are technical rather than conceptual in nature.
They are presently being addressed at ANSTO and elsewhere with the application of various novel numerical analysis techniques backed by experimental validation, as well as the development of intricate robotics, specifically relating to remote operation and advanced manufacturing.